Lo studio e la ricerca di nuove finiture e rivestimenti per Cappotto Termico, dai colori alla struttura superficiale, dalla modularità alle dimensioni, hanno portato ad un’importante innovazione di tutto il sistema rispetto alle soluzioni tradizionali.
Dalla sua origine l’isolamento termico degli edifici, in particolare in Italia, ha avuto un difficile rapporto con il progettista in merito alla sua particolare limitatezza di possibili finiture e rivestimenti per Cappotto Termico.
Per anni l’indicazione, la proposta dei produttori ed i suggerimenti riportati su tutte le schede tecniche dicevano, riferendosi al Rivestimento di Finitura (RPC) di un Cappotto: “lo spessore minimo deve essere compreso tra 1,5 e 2,0 mm secondo la struttura del rivestimento ed il suo colore deve presentare un Indice di Riflessione non inferiore a 20÷25%”
Questo diktat, questa imposizione vale ancora oggi per la maggior parte dei sistemi a Cappotto dotati di un Benestare Tecnico Europeo ETA n°…… ma in questo ultimo decennio è stato profuso un grande sforzo da parte dei Produttori di sistemi per offrire soluzioni estetiche ed architettoniche che andassero a soddisfare le differenti esigenze dei Progettisti.
È interessante vedere come lo studio e la ricerca di nuove finiture e rivestimenti per Cappotto Termico – colori, struttura superficiale, modularità etc – hanno portato ad uno sviluppo del pacchetto Cappotto, del KIT, in cui sono stati apportate importanti varianti, rispetto alle soluzioni tradizionali, nella scelta dell’isolante e delle lavorazioni apportate su tale elemento, dello strato armato di supporto alla finitura, del metodo di tassellare e di applicare la finitura anche in strati successivi.
A fronte di questo sviluppo si sono affermati sistemi dotati di specifico Benestare Tecnico Europeo al fine di garantirne la loro idoneità applicativa.
ATTENZIONE: se si intende progettare una facciata isolata a Cappotto con superfici di particolare disegno, struttura o di finiture specifiche (ceramiche, pietra, etc), si deve assolutamente verificare l’esistenza di sistemi che rispondono alle caratteristiche che si desidera ottenere e se ne deve adottare il “KIT” nella sua completezza, senza trascurare nessun dettaglio costruttivo previsto dal produttore del sistema.
Ciò premesso, i rivestimenti per Cappotto Termico oggi si possono distinguere sostanzialmente in:
- Rivestimenti continui di varia natura, di vario design e di varie caratteristiche prestazionali
- Rivestimenti modulari anch’essi di varia natura e forma
Vediamo come queste finiture si sono sviluppate alla ricerca di soluzioni estetiche in grado di soddisfare le esigenze architettoniche dei progettisti, che sono giustamente sempre più esigenti in termini di geometrie e colori.
I fattori sui quali le aziende produttrici si sono concentrate possono essere così elencati:
- Il COLORE di differenti tonalità e non più vincolato ai valori di IR
- La PULIZIA delle superfici ed il mantenimento nel tempo di tale caratteristica anche in ambienti particolarmente ricchi di inquinanti
- Il DESIGN delle finiture
- I RIVESTIMENTI MODULARI
- Le SUPERFICI MOSSE
- DECORI IN FACCIATA
In contemporanea si sono sviluppate tecnologie adatte dei componenti dei sistemi stessi (KIT) al fine di assicurare un supporto idoneo alle varie soluzioni di finitura.
- COLORE
Come accennato poco sopra in merito allo sviluppo del colore nei rivestimenti per Cappotto Termico, i vari produttori hanno percorso varie strade intervenendo non solo sul rivestimento ma anche sui componenti del sistema.
Una prima strada è stata quella dell’impiego di cosiddetti “Pigmenti freddi” ossia pigmenti in grado di aumentare sensibilmente i valori dell’indice di riflessione IR della finitura prodotta in colori scuri,colori che per loro natura sono particolarmente soggetti ad elevato assorbimento di calore e quindi con un basso IR
Questi pigmenti sono in grado di ridurre le temperature superficiali del rivestimento esposto a SUD e OVEST di circa 12°÷20°C con l’effetto di stressare molto meno il sistema Cappotto in particolare la sua “crosta” esterna protettiva e l’isolante sottostante.
Il grafico sotto riportato evidenzia come l’impiego di un pigmento nero ad elevata riflettenza (pigmento freddo) consente a colori particolarmente scuri di avere un IR accettabile per il suo impiego su Cappotto.

Spesso, per assicurarsi una vita del sistema paragonabile a quella garantita dai colori ad alto IR, oltre all’impiego di pigmenti freddi, il sistema Cappotto che adotta colori a basso IR è composto da strati differenti rispetto ai sistemi “normali” ( solo a titolo di esempio: rasature di resistenza meccanica particolarmente importante e a volte additivate con fibre di carbonio, spessore elevato delle rasature, reti di armatura di maggiore resistenza, eventuale impiego di isolanti fibrosi, etc).
In ogni caso va contattato il produttore che detiene il Benestare Tecnico del Sistema sia per approfondire le possibilità cromatiche sia per progettare l’intervento in modo corretto in materiali e posa.
Il colore chiaro quale limitazione alla creatività estetica non è più così assoluto, permane il requisito, necessario per l’applicazione di un rivestimento “scuro”, che faccia parte integrante di un KIT che ne consenta l’impiego
- La PULIZIA delle superfici ed il mantenimento di tale caratteristica anche in ambienti particolarmente ricchi di inquinanti.
I primi problemi sui rivestimenti per Cappotto Termico si sono presentati con la formazione di alghe e muffe superficiali in particolare sulle pareti rivolte a Nord e in zone prossime a zone ricche di vegetazione.
Per un approfondimento specifico di questo problema e delle soluzioni adottate dai produttori di sistema si rimanda al capitolo “ALGHE E MUFFE SUL CAPPOTTO TERMICO” di prossima pubblicazionel |
Il vero sviluppo tecnologico si è per altro manifestato nella ricerca di soluzioni che fossero in grado di mantenere pulite le superfici e vivi e limpidi i colori originali.
Per ottenere questi risultati i produttori hanno percorso strade differenti, non necessariamente uniche, che si possono così riassumere
- formulazione di finiture con una particolare combinazione di pigmenti, cariche minerali e resine ricavate per polimerizzazione dalla silice o ossido di silicio e da resine siliconiche che consentono di mantenere le facciate pulite per periodi di tempo molto lunghi, riducendo l’assorbimento delle particelle di sporco e favorendo lo “scivolamento” dell’acqua meteorica che aiuta a mantenere pulita la facciata.
- formulazione di finiture dotate di componenti in grado di decomporre le sostanze organiche che vengono a contatto con i rivestimenti per Cappotto Termico, contribuendo sia al mantenimento di una superficie pulita che al contrasto dell’inquinamento atmosferico.
- inserimento, nei prodotti di finitura, di additivi sostenibili e rispettosi dell’ambiente atti a resistere all’infestazione di alghe e muffe – prodotti certificati antialga.
- trattamento finale, delle superfici rivestite, con un film in grado di conferire ai rivestimenti applicati la corretta “scivolosità” che consente all’acqua meteorica di pulire le facciate.
Un’attenzione e un consiglio:
nella realizzazione di nuovi davanzali per le aperture, in grado di contenere lo spessore del Cappotto applicato, si consiglia di adottare l’accorgimento di convogliare l’acqua meteorica, che dilava il davanzale stesso, verso l’esterno e non farla gocciolare sulla facciata provocando brutti “baffi” laterali ai davanzali
- Il DESIGN DELLE FINITURE E DEI RIVESTIMENTI PER CAPPOTTO TERMICO
Lo sviluppo di finiture e di rivestimenti per Cappotto Termico di particolare aspetto, sia materico sia di colore, è un fatto comune a tutti i produttori di sistemi a Cappotto.
Questo sviluppo deriva sostanzialmente dalla ricerca di finiture “nuove” in grado di offrire al Progettista soluzioni che soddisfino la sua ricerca estetica.
Le superfici delle facciate di edifici privati e pubblici rivestono un’importanza e un significato particolare e non potevano fermarsi a finiture di struttura semplice e di colore scontato.
Ecco quindi lo sviluppo di superfici caratterizzate da strutture complesse, nuove e da texture uniche, ruvide o lisce, lineari o di particolare grafica, alcune riprendendo la composizione di pietre, graniti o marmi, altre riprendono l’aspetto dei cementi faccia vista oppure di superfici metalliche.




Queste finiture vogliono una particolare capacità applicativa e la Direzione Lavori si deve sincerare della abilità e idoneità a queste applicazioni da parte dell’addetto alla posa in opera.
- I RIVESTIMENTI PER CAPPOTTO TERMICO MODULARI
Si può affermare che in Italia le prime richieste di finiture costituite da rivestimenti modulari sono iniziate quando si è incominciato ad intervenire su edifici con rivestimento in clinker. I progettisti ricercavano una soluzione che assicurasse un buon recupero energetico – un Cappotto – senza dover rinunciare alla finitura originale.
Il clinker è stato il rivestimento distintivo degli edifici in particolare nella zona del milanese a cavallo del recente dopoguerra: noto è il progetto dell’Architetto Muzio, Palazzo dell’Arte di Milano dove l’uso di questo materiale rivedeva la tradizione del cotto in chiave moderna.
Il clinker è stato prodotto solitamente in piastrelle di varie misure e di varia geometria incollate direttamente alla superficie muraria: si trattava di una pelle, un involucro esterno che può assumere aspetti e forme più svariate.
Le soluzioni che sono emerse quando sono stati studiati i rivestimenti per Cappotto Termico tipo clinker, hanno varianti sia nel tipo di finitura che nel “kit” che sostiene questo rivestimento modulare con piastrelle di piccolo formato (attorno a 12,5×25 cm):
- alcuni sistemi hanno percorso l’impiego di rivestimenti simili al clinker ma di fatto costituiti da listelli in granuli di laterizio naturale o pietra naturale ricomposti con minime percentuali di resina acrilica
- altri sistemi hanno adottato rivestimenti a basso spessore in laterizio cotto o clinker tradizionale modificando e migliorando la zona di aggrappo tra pannello isolante e strato rasante per favorire una migliore e maggiore adesione tra i due strati

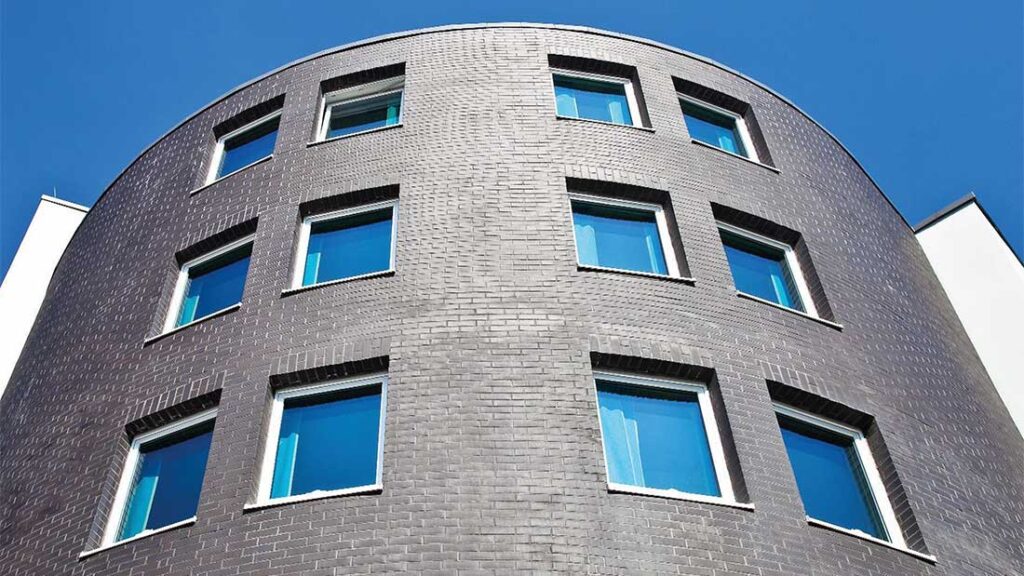
Altre soluzioni emerse hanno rivolto l’attenzione sui rivestimenti per Cappotto Termico modulari cosiddetti di “grande formato” (attorno a 50 x 100 cm).
In questi casi l’attenzione del produttore si è concentrata sulla composizione del “KIT” al fine di garantire il buon funzionamento del sistema con particolare occhio di riguardo al pannello isolante, alla sua geometria, alle lavorazioni superficiali per assicurare una straordinaria adesione isolante/rasatura, al tipo di rasatura armata e al tipo di rete di armatura, al fissaggio meccanico del pannello e altre attenzioni specifiche.
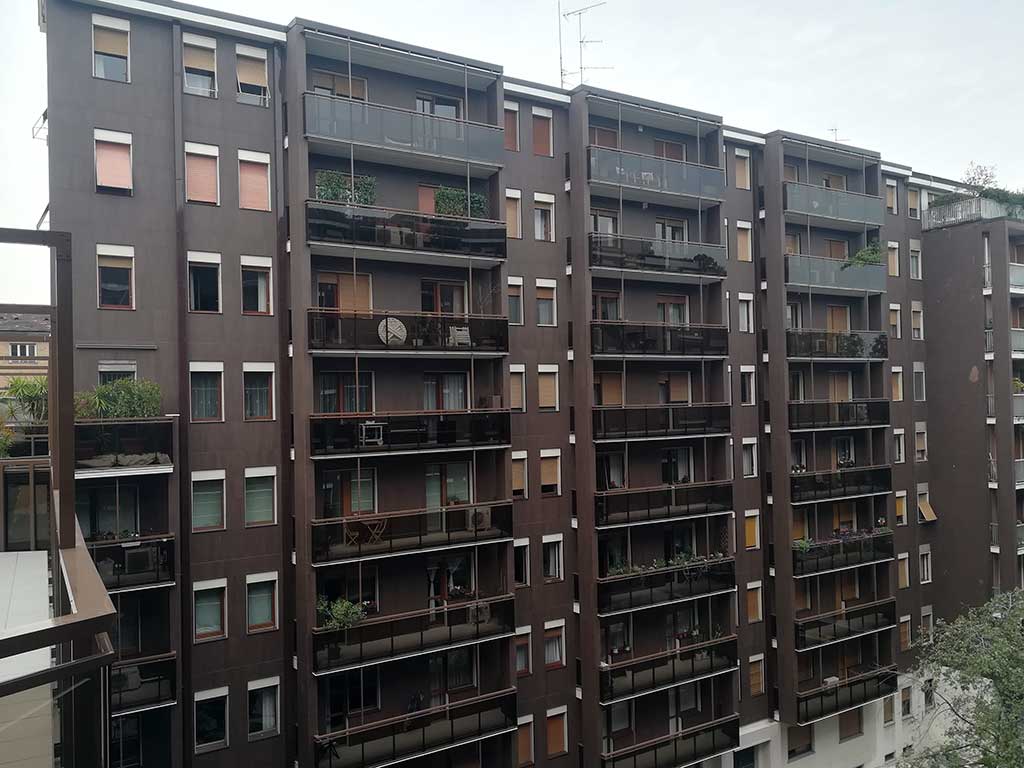

Esempio di rivestimenti per Cappotto Termico di grande formato nell’intervento di Via Foppa 7, Milano.
Per ultimi, ma non per importanza, i sistemi che riprendono il mattone facciavista o pietre ricomposte di varie forme e dimensione
I sistemi presenti sul mercato prevedono finiture con listelli di spessore massimo 1,5/2 cm in cotto o in granuli di laterizio naturale ricomposto con minime percentuali di resina acrilica con o senza trattamenti protettivi di finitura



E’ importante a conclusione di questo paragrafo sui rivestimenti per cappotto termico modulari, precisare che una grande attenzione va posta nella scelta e nella verifica, sul cantiere oggetto di intervento, dei fissaggi meccanici (tasselli).
Non è pensabile di realizzare sistemi con rivestimenti per Cappotto Termico come quelli sopra illustrati, senza aver fatto accurate prove di strappo dei tasselli, nella misura che verrà adottata sulle pareti dell’edificio oggetto di intervento.

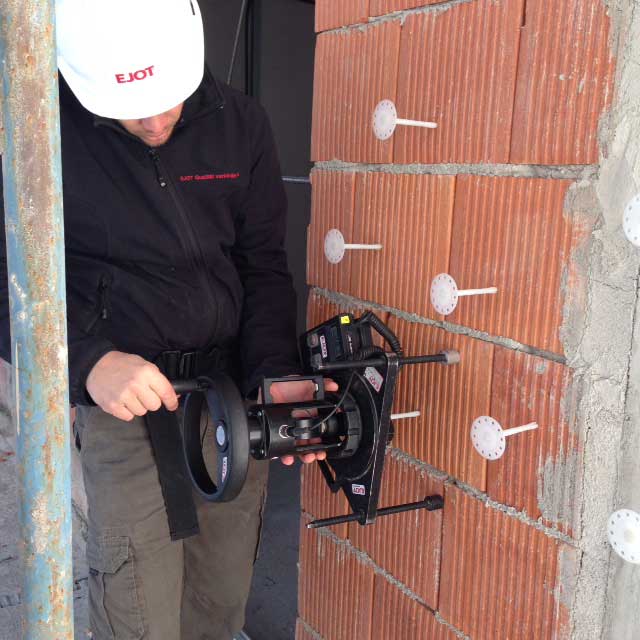
- Le SUPERFICI MOSSE
Frase tipica che circolava negli anni ’90: “Con il Cappotto si realizzano solo facciate piatte ed edifici “scatola””

Queste facciate sono state realizzate grazie alla straordinaria progettazione dell’Arch. Cino Zucchi e sono l’esempio più significativo di come con il Cappotto si possono modellare le superfici metro per metro determinando un grande impatto architettonico. Intervento in via Frassinetti 25, Milano

Alla base di queste scelte architettoniche c‘è la considerazione che il pannello isolante non è solo un elemento STANDARD, lo si può “modellare” per ottenere superfici che giocano con il sole ombreggiando le facciate di minuto in minuto in modo differente.
Solo a titolo informativo va precisato che, su superfici di tale geometria è più che indispensabile impiegare rivestimenti per Cappotto Termico che abbiano buone caratteristiche di autopulenza.
- DECORI IN FACCIATA
Oggi esistono soluzioni tecnologiche coibentanti tali da riprendere fregi e contorni tipici di facciate di particolare pregio. Si tratta di elementi preintonacati da applicare sul Cappotto a rasatura armata ultimata e prima di realizzare il rivestimento di finitura.
Le forme e dimensioni sono molteplici e possono essere realizzate su misura, per dimensioni e disegno. Un esempio di queste applicazioni è la riqualificazione energetica dell’edificio storico sito in Foro Bonaparte 16, Milano, nel quale è stato possibile applicare i sistemi di isolamento esterno su facciate caratterizzate da numerosi elementi decorativi, senza deturparne l’aspetto originale.



Rileggi i capitoli precedenti:
- Guida essenziale sul Cappotto Termico, la presentazione ufficiale
- CAPITOLO 1 – I COMPONENTI DEL CAPPOTTO IN EDILIZIA
- CAPITOLO 2 – L’APPLICAZIONE CORRETTA DEL PANNELLO ISOLANTE TERMICO
- CAPITOLO 3 –RASANTE, RETE D’ARMATURA E FINITURA DEL RIVESTIMENTO A CAPPOTTO DEGLI EDIFICI
- CAPITOLO 4 – LA TRASPIRABILITÀ DELLE PARETI COIBENTATE
- CAPITOLO 5 – UMIDITÀ NEGLI AMBIENTI E RIVESTIMENTO A CAPPOTTO
- CAPITOLO 6 – NODI CRITICI E PARTICOLARI COSTRUTTIVI SULLE FACCIATE DEGLI EDIFICI
NOTE DELL’AUTORE – Ing. Carlo Castoldi – Comitato Tecnico Scientifico di Rete IRENE, è stato membro della Commissione UNI per Cappotto e Pareti Ventilate e della Commissione Tecnica Cortexa (Consorzio per la diffusione della cultura del sistema Cappotto).
Sembra ottimo